KMUW Membership Drive
Welcome to
Brushy Creek Pottery & Botanicals
We are very pleased to be a part of the
Public Radio membership drive.
Through your membership and continued support, you help keep this wonderful style of programming alive.
|
Public radio is part of everyday life here at Brushy Creek. We enjoy the antics of The Prairie Home Companion and Car talk. The soothing and stimulating sounds of the classical music, as well as the exciting and soulful sounds of Jazz and Dixie inspire our art form and subsequently, us. The benefits we receive from listening to Public radio are entertaining, cultural, historical and educational. In fact, stations like KMUW,
offer an education in the art of culture and music.
We on the other hand, offer and education in the ART of Pottery.
For your pledge you will receive a part of our art form.
A hand thrown mug with thumb rest
Holds approximately 12 ounces
Wood fired
Each mug is a unique piece that is part of a limited edition of 500
Made exclusively for KMUW and this pledge campaign.
A collectible, each one is hand signed, dated and numbered by the artist.
Meet the artist
Ken George
Earth, water, air and fire combine to make my pottery.
Raw clay transformed on a potter's wheel then set aside to dry. Soon the leather-dried piece has artistic impressions and glazes for colors and then fired with wood to complete the pot. This is the evolution of the pots found at Brushy Creek Pottery.
Ken's pots are all hand crafted and wheel thrown. A native Missourian who has visited many places around the globe and yet, Ken, has kept the inspiring beauty of the Ozarks close to his heart. This is apparent in his work and artistic impressions. Each piece Ken creates is a work of art also inspired by the history and timeless beauty that pottery represents. Ken's profound interest in the ancient history of the art is what inspires him to wood fire his pieces. All of the glaze affects he creates can only be achieved in a wood-firing environment, much like the firings of ancient times. Many of the glaze colors he chooses are also representative of ancient art of pottery. (To read more about Ken and his art, follow this link).
Ken and his wife Vickie offer education in the art of pottery via their web site,
Pottery the ART.
It is filled with information and demonstrations about pottery. On line visitors have the ability to send questions and obtain answers about the art via the internet.
You will have a unique opportunity to see (via this page),
the process and stages it took to create the KMUW Mugs
Pottery process:
Throughout this page you also will find active links.
These links will direct you to the topic discussion on our Pottery the ART site.
Follow the links to learn more about each of the pottery processes.
The process begins by collecting
the wood for the kiln firings
Inside the kiln shed at Brushy Creek Pottery
Collecting and stacking wood to dry for the kiln is a year long job.
Ideally, the wood needs to dry for 1 to 2 years for optimum performance.
Before putting the slabs of wood in the kiln each one must be split.
Wedging
Preparing the clay for throwing by wedging
Process of eliminating air bubbles and making the clay a uniform consistency for throwing.
Important process: If air bubbles are present in the clay,
chances are the piece will crack or blow up during any stage of the firing processes.
To Wedge
Start by compressing the clay downward
on your wedging table.
Using a rocking motion
continue compressing the top of the clay inward,
making sure you are not pushing air into your mound of clay.
To read more about this process follow the link to Wedging
|
To begin the throwing process:
Clay balls are cut, weighed and wedged into 1 1/2 pound balls.
Each mug begins at the 1 1/2 pound weight and will shrink approximately 13% during the overall pottery process.
|
|
Before beginning, imagine the piece you are wanting to throw.
We begin the process by placing the clay ball in the center of the wheel head.
The clay must then be centered.
Centering is the process of securing the clay to the wheel head and forming the center of the piece.
|
|
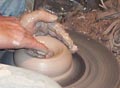 The next step in developing your piece is establishing the bottom.
In these images: The artist is using his fingers to press down on the clay while the wheel is turning.
He will continue pressing down until the desired thickness is achieved.
|
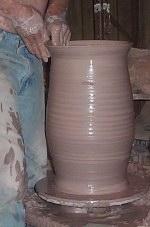 To develop the walls of the pot; the artist will use his fingers as guides pulling the clay upwards creating the desired height.
This process is used on each wheel thrown piece.
|
The height in the pot on the left was achieved with three pulls upwards.
Normally it takes three full pulls to create a pot.
|
These images are the second and third pulls in one of the KMUW mugs.
|
|
|
Once the mug is thrown; a potter's knife is used to guide the pot away from the wheel head and placed on a ware-board to dry.
|
Trimming
Once the mugs are dry enough to handle they are ready for trimming.
|
In both of these images:
Ken is trimming excess clay away to give a nice light feel and balance to his mugs.
|
|
Ken's style of glazing and firing require a special foot on his pieces.
The foot is the bottom and very edge of the pot.
He creates a foot that will allow his high fired glazes to flow to the bottom of the pot and pool around the edges.
|
Without this style of foot; the glazes would flow off the pots while at a liquified stage during the actual firing.
|
|
|
The final stage in the trimming process:
Ken signs, dates and numbers each of the pieces by hand.
|
KMUW Logo
|
Ken hand carved a wooden relief stamp for the KMUW logo.
|
Each logo was hand made using the method shown
|
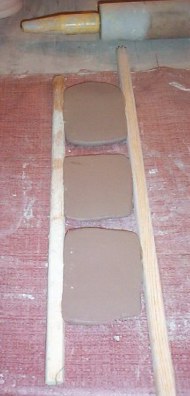 Each logo began as a slab as shown in the image on the left.
Using a rolling pin and guides; the slabs were rolled to the desired thickness.
|
|
Once rolled, the slab is placed over the relief stamp. The rolling pin is gently ran over the slab a few times leaving the impression of the KUMW logo.
|
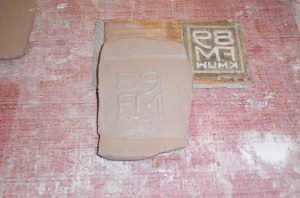 The logo is removed from the stamp and placed on a ware-board to await assembly on a mug.
|
|
Adding the Logo to the mugs
|
Before attaching the logo to the mug; it must be trimmed to the correct size and shape.
|
|
A fork is used to score the mug before applying the logo.
|
|
Clay slip is used as an adherent.
The slip is liberally applied using an artist's brush.
Mix a small amount of clay, with just enough water, to form a batter like consistency.
|
|
The logo is then placed on the mug in such a way as to eliminate air bubbles from becoming trapped behind it during the bisquing and firing stages.
|
|
After applying the logo the edges are wiped clean of excess clay slip. The mugs are placed on a covered ware board to dry for a few hours before applying the handles and thumb rests.
|
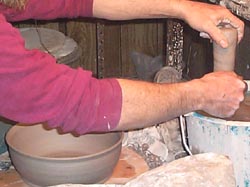 Ken begins the handling process by hand pulling each handle.
He starts with a small amount of rolled clay,
|
He pulls the clay until it forms his desired width and length.
|
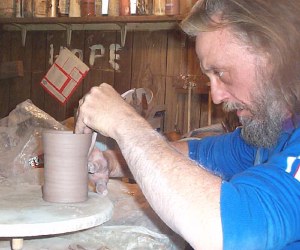 Using the same method as the logos:
The mugs are first scored in the spot the handle is to be applied.
Clay slip is used to adhere the handle.
|
Each handle is hand formed and attached to the mug.
|
Thumb Rests
|
Ken prefers to add thumb rests to his mugs.
|
|
He forms a small ball of clay, shapes it and then adheres it to the mug with clay slip.
Once the thumb rest is in place,
|
Each mug is set aside to dry to the bone dry stage
before on to the next step,
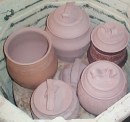 Pre cooking stage for high fired pottery.
|
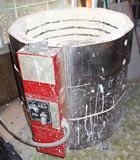 Electric bisquing kiln
|
We bisque our pottery to 1900 degrees F.
Bisquing burns the organics and molecular water out of the clay.
The clay body will readily absorb glazes at this non vitrified stage of the process.
|
|
|
Bisquing also makes the clay hard, yet porous. Notice the color change in the clay body after bisquing.
|
|
Once Bisqued:
To achieve the appearance Ken wants for the KMUW logo's,
Iron Oxide is applied using either a sponge or artist's brush.
|
Next the mugs are glazed
|
Glazes are the potter's pallet of colors
|
Glazes are applied in many ways.
Ken formulates all of his own glaze recipes. The recipes are made specifically for high temperatures in a wood firing atmosphere.
They can be applied in many ways:
Dipping
Painting
Trailing
Just to name a few
|
|
|
There are many various techniques used in firing pottery.
We prefer to wood fire. Wood firing is one of the most difficult of all firing methods.
Ken hand built and designed our wood firing kiln. It is a sprung arch design with over 3,000 fire bricks.
This is the front of the kiln, the opening is the door which is bricked up during the firing process.
|
|
This is the roof of the kiln. Notice the arch in the brick design. You can also see the kiln shelves the mugs will be placed on during the firing. Stilts are used to hold the shelves in place and for stacking.
This is a cone pak.
Each one of the cones will melt at different temperatures during firing to allow the potter to see how hot the kiln is.
|
|
There are two stoking holes on the side of the kiln. The kiln must be stoked and wood added throughout the entire process.
Temperatures are gradually brought up just as in an oven, by adding wood and adjusting the flow of oxygen.
The mugs were fired approximately 8 hours and will use about 1/2 cord of wood for the entire process.
After the firing is completed the holes are covered and the kiln will be allowed to cool for about 18 - 24 hours before opening.
|
Enough time must be allowed before un bricking to prevent the pottery from cracking by exposing it to cooler air. Just like glass, the pottery will crack when introduced to extreme temperature changes.
Once cooled the door is unbricked and the pottery is removed
We invite you to follow the links provided to read more about the pottery
steps discussed on this page
&
ART of Pottery.
Thank you for visiting with us
&
for your support of the arts, public radio
and the KMUW membership drive.
We invite you to follow the links below to learn more about us and our art.
Ken and Vickie George
Brushy Creek Pottery & Botanicals
Pottery the ART
|